摘要:一个新的范例出现了,在批量数据处理过程中取消了中间环节,因此消除了通过中间应用、网关和协议转换传递数据过程中发生的潜在错误和定时问题。本文探讨将数据直接从数据源传输到最终使用点的方法,即无论是从操作台、控制器或者是从磁盘媒介得到的数据,不再通过中间数据库、应用或其它“中间环节”。根据需求文档精心构造设计,数据生产者将直接和数据消费者通讯。作者将其命名为“直接数据处理模型(Directed Data Transaction Model)”来描述这个结构化方法。
直接数据处理模型可以有效地把控制软件分为机器级控制需求、单元级控制需求和企业级控制需求,而不是像现在的方法,让数据在所有控制级别的所有控制单元上都有效。直接数据处理基于数据生产者和数据消费者形成的需求构建控制系统的设计方案,包括硬件和应用软件,以符合这些规定需求。
关键字:数据处理,网络,可靠性,效率,批量记录
前言
ANSI/ISA 95.00.03-2005[1]定义行为的多级功能体系由5级组成,分为0级到4级。每一级包含一个时域(毫秒、秒、分钟、小时等等)、一个活动域(调度、生产、监测等等)和一个数据域(存储水平、生产记录、传感器的值等等)。
在现代控制系统中,设计应用程序以最少的重叠对体系中特定级的特定需求寻址。例如,1级的应用程序常常在固件或者专有的硬件程序空间中编码,即PLC和DCS系统。控制工程师创建程序或配置模块和程序单元,然后下载程序或配置到控制器上。在2级应用程序空间, SCADA和DCS供应商提供大量应用程序,作为客户端-服务器应用程序存储在商用计算机的硬件上。图形、应用程序和数据服务通常存储在服务器级别的计算机,它和其他客户端工作站一起放置在最终使用点的厂房地面上。网络把1级和2级应用组件互相链接到一起,因此形成一个节点网络,在这里数据和应用可以共享资源、数据值和信息。
在3级领域中,来自1级和2级系统的数据被生产操作管理程序共享。这个程序用来设置和控制工作流程、执行详细的生产调度和维护数据记录,用于报告和生产优化。3级应用程序通常存于一个单独的网络中,因为在3级和2级/1级应用程序之间流通的数据处理的结果和预期相反。
理论上,这个高度集成的数据和应用程序网络在工业化环境中执行,有高可靠性(>99.99%)和低出错率或不需要操作者和维护者的干预。虽然有这样的高可靠性,预计仅仅由网络硬件的错误而导致的停机时间一年有一小时。最近的一次调查,8%的人指出,他们每周都遇到网络问题,另外11%的人指出他们的网络出现小事故的数字在上升[2]。一个典型的批量控制系统体系结构如图1所示。
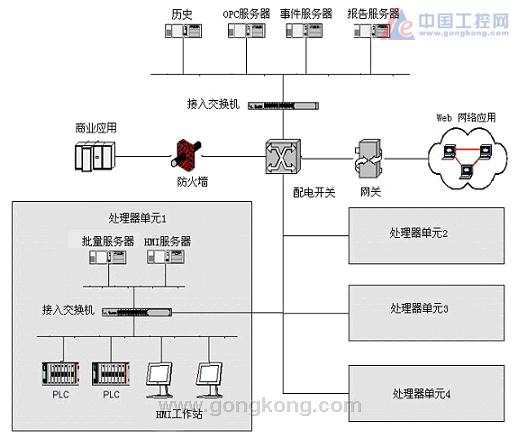
图1 简化的现代批量控制网络体系结构
一、批量控制系统中的数据处理
图1描述的批量控制系统体系结构似乎有很高的效率。基于单元的功能由低处的自动化“岛”(处理单元1)处理,一般服务功能由高处的“岛”处理。然而,即使在这个简单的实例中,尽管所有系统厂商都声称为数据处理提供一个可靠且有效的体系结构,大部分控制系统的可靠性却远小于理想情况。这主要是由于以下诸多因素[2],包括:
- 源自多个供应商的应用程序在一起未必能顺畅工作;
- 由于劣质的网络设计产生的网络负载问题,产生“数据爆炸”或“数据溢出”;
- 操作系统程序错误;
- 硬件不兼容,设备驱动的限制,等等;
- 应用程序间脆弱的通信连接(DCOM,等等);
- 应用软件的限制:太多的处理,内存或磁盘空间限制,等等;
- 应用程序间不同步或需要持续的干预;
- 内存泄漏,DLL文件不兼容,或者内部软件异常;
- 程序超出它们预期的限制和使用;
- 应用程序、配置或操作系统的改变没有得到完全测试;
- 内部应用软件错误。
供应商、系统集成商和最终用户同样可以通过日常工作以消除上面列出的问题。然而,因为供应商急于发布软件更新;最终用户想要额外的功能,且希望用最少的测试和停工时间安装软件更新;系统集成商被要求在更短时间内提供更大范围的服务,上面列出的问题在未来十年仍然是系统可靠性的限制。
即使不是大多数,很多批量控制系统目前用于工业中的过程控制。在这些工业中,过程中的数据采集、操作者行为的报告、警报、事件和批量控制程序操作顺序的捕获非常关键。即使这些工业不需要数据达到100%的完整性,对于优化、高效计算和批处理趋势比较,准确的数据记录仍是至关重要的。
上面列出的问题可以在很多方面导致数据采集和历史问题。程序错误导致丢失数据是很常见的。由于传输错误或者是控制器保持在最后一个值引起的数据被“冻结”,可能造成曲解数据报告并导致调节问题。每个制药、生化、食品和饮料以及医学设备公司都可以指出一个或多个由于上面列出的控制系统错误所导致的数据未被采集的情况和案例。
大部分由于数据处理和传输问题导致的数据记录错误不是因为从数据源得不到数据。历史数据“缺口”的产生常常是因为数据值在从0/1级传感器和数据源到控制记录数据的2级或3级应用程序空间中的应用程序的过程中变化的问题引起的。
如果把图1中的批量控制系统体系结构重画成表示系统数据处理的示意图,它就变成图2。这个图显示在批量控制系统中不同的设备和应用程序间通常是如何处理数据的。
数据处理问题出现在数据从一个应用程序到另一个应用程序传送路径的交接点处。例如工业现场产生的温度测量和操作输入(图2中的‘A’),数据被测量或由自动控制器打包后放到数据总线或网络上广播(B)。其值通过网络被SCADA程序或DCS程序捕获。在此数据上附加上输入标记、添加一个时间日期图章、验证数据并把数据传送给历史应用程序(C和 D)。历史应用程序依次检验数据所属的历史群组,把数据值存储到存储缓冲区,并定时地把数据写入磁盘(E) 。
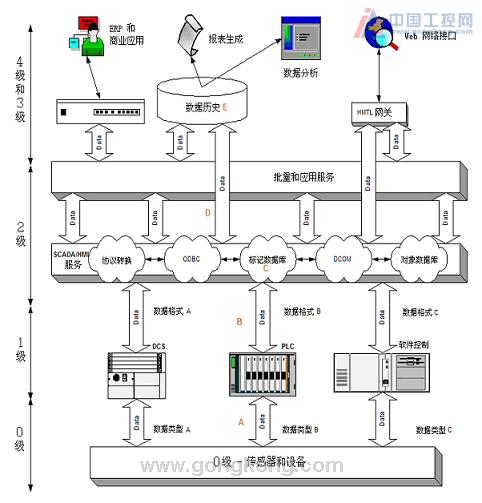
图2 一般的批量控制数据处理示意图
上文描述的数据处理是典型的,但是在给出的实例或应用程序中可能更加复杂。在数据源和数据的最终存储/文档/应用之间可能存在许多额外的处理。更复杂的情况下,数据可能还会经过从数据源到最终使用之间传输时的协议转换。即使在上面简单的实例中,经常由于测量、程序错误、协议错误和磁盘子系统错误发生问题,而这仅仅是一小部分。
二、直接数据处理模型简介
一个新的范例出现了,在数据处理过程中取消了中间环节,因此消除了数据通过中间应用、网关和协议转换时发生的错误。在这个模型中,数据直接从数据源传递到最终使用的点上,不管它是一个操作控制台或者磁盘上的历史数据文档。数据不通过中间数据库、协议转换、或者中间程序。数据生产者直接与数据消费者通信。
获得了几个新的方法,包括:
- 在1级设备上使用硬件接口允许数据直接传输到3级应用程序上。
- 1级采集的实时生产数据,随后批量传输到3级的数据历史服务器上。
- 在自动控制器中使用嵌入的2级和3级的应用程序,从而取消了网络处理实时数据的需求。
- 使用单独的程序处理过程可视化、批量控制和生产操作管理,因此无需单独的HMI和生产管理软件。
每个新方法提供一个新的过程控制设计使用的范例,这个方法被作者称为直接数据处理模型。这种方法有效地把控制程序分为机器级控制需求、单元级控制需求和企业级控制需求。而不像现在的方法,让数据在所有控制级别的所有控制单元上都有效。直接数据处理结构要求在数据生产者和数据消费者以及控制系统的基础上,包括硬件和应用软件来满足特定需求。这个方法独立于任何供应商提供的硬件或软件。虽然这里的讨论将聚焦在批量控制和批量数据,但是这些方法可以应用到任何过程。
这个方法的应用受到许多大学在多重处理上的生产者-消费者模型和多处理器计算机系统上资源共享方面研究的启发[2]。本文的作者相信,在过程控制系统及高速多处理器计算机系统中,高效的数据生产和消费是并行的。
在过程控制和多处理器计算机系统中,数据应尽可能在靠近数据源的地方使用,以使与应用程序错误有关的问题、传输错误、协议转换错误和硬件错误减少到最小的程度。
三、直接数据处理模型实例
利用上面的例子(最后存储在数据历史服务器上的厂房地面温度传感器产生的数据)我们应用直接数据处理模型,看看这个体系结构是如何提高数据传输的效率和可靠性。假设温度测量仅仅是一个监测点,也就是说它不需要控制回路,但是需要实时监测。还假设需要把数据放在过程图形显示器上,需要每十秒采样并存储在数据历史服务器中。过程单元由PLC控制,并有如图2所示的一个HMI和批量监控系统。
在试图构建解决方案之前,注意这个模型的应用程序要求设计工程师生成一个需求的顺序集。为此,工程师需要了解批量控制系统,并把所有的数据生产者和数据消费者列成表格。对于我们的问题,温度传感器是数据生产者,有3个消费者,如下图所示。为了说明,附加了其它信号。
项目 |
生产者 |
消费者 |
温度 |
RTD传感器-TE1004 |
PLC I/O 子系统 |
|
|
HMI图形显示器 |
|
|
数据历史服务器 |
流量 |
质量流量-FE1001 |
PLC I/O 子系统 |
|
|
HMI图形显示器 |
|
|
数据历史服务器 |
|
|
PLC 控制回路 PV |
流量控制 |
控制回路输出 |
FV 1001 |
从配方提取的SP流量 |
批量控制服务器-配方 |
PLC 控制回路 SP |
记住,在传统控制系统体系结构中,从厂房地面到数据历史服务器,温度测量要经过5次处理:
1. 传感器的值输入PLC并把测量值存入I/O数据表中;
2. 梯形逻辑、功能模块、等等,用于转移数据到内存区域以便成块读取到HMI服务器;
3. HMI服务器使用OPC、等等,从PLC内存中读取温度测量值并把该数值存储到活动的标记数据库上(本地的或全球的);
4. 每隔5秒钟HMI服务器扩展ODBC包把温度测量值转移到数据历史服务器上;
5. 数据历史服务器检测存在的数据值并把数据存储到内部数据库或磁盘文件上。
附加的数据处理可能需要更加高效的分布式系统,系统使用源自不同供应商的软件组件,或者需要特殊格式或特殊协议的应用程序。
使用直接数据处理模型时,一旦确定了数据生产者和消费者,需要的体系结构就可以研制出来。最终,传感器和控制元件都会嵌入智能使得它们可以启动数据传送。到那时,PLC或DCS控制器(或其它智能 I/O子系统)会要求能够读取、测量、并且使传感器的输入能用于控制回路和其它消费者。因此,在这个例子中,上面的数据处理1将仍然是需要的,尽管在PLC中不再需要温度测量。
温度数据的另外两个消费者是HMI图形显示器和数据历史服务器。在上面列出的处理中,如果PLC到HMI服务器的链接被断开了,HMI子系统和数据历史服务器都不会接收到温度数据。这只是此数据处理5个可能的故障点之一。只有当全部5个处理都正常时,数据历史服务器才能接收到数据。前面曾提到过,在规范的工厂环境中,这个数据的历史非常关键(需要灵活调节)。在产生数据的点(TE1004)和消费数据的点(数据历史服务器)之间共有五个处理,有很严重的数据丢失风险。
对于温度测量的例子,一种直接数据处理模型的可能应用情况,使用可以商业供货的产品进行温度测量,其数据处理的示意图如图3所示。图4表示使用这个模型之后,最终达到的网络体系结构。在这个例子中,PLC已经嵌入了嵌入式数据历史模块和数据库处理模块。
嵌入的数据历史模块可以在配置的长达几天的时间段内存储数据值。数据可以在本地缓存并且定时转移到中央数据历史服务器上。在传输出错时,另外可选择的配置可以通过轮询本地缓冲区的方式传送数据。
数据库处理模块可以直接从PLC内存读取数据,形成数据处理包,并把这些包直接传送到HMI标记数据库上。这个模块还能用来把操作行为和事件数据存储到批量服务数据库上。
直接数据处理模型的应用是很直观易懂的:1)确定数据生产者和消费者;2)选择允许在数据生产者和消费者之间直接进行数据处理的硬件组件;3)利用选择的硬件组件构造批量控制系统结构,以提供所有需要的数据处理路径。作为应用这个模型的结果,在温度测量这个实例中,数据处理的数目从5减小到3。减少交接点可以降低丢失数据的风险和增加过程控制系统的整体可靠性。再者,第一个处理(A)是在I/O子系统中对工厂地面变量进行测量,这是非常可靠和稳妥的处理。图2中的3个中间处理(B,C,和D)被取消了,并且被一个单一的处理(图3中的B)所取代。由于数据被嵌入的数据历史模块在本地缓存,处理时间就不那么紧张了。
为了适应直接数据处理模型,网络体系结构无需显著改变。增加了4个LAN 连接以适应 PLC子系统中增加的硬件模块。巧妙地使用冗余交换和VLAN可以提高效率和可靠性。直接数据处理模型产生的体系结构为数据历史处理和HMI标记服务处理分别定义专用的 VLAN。
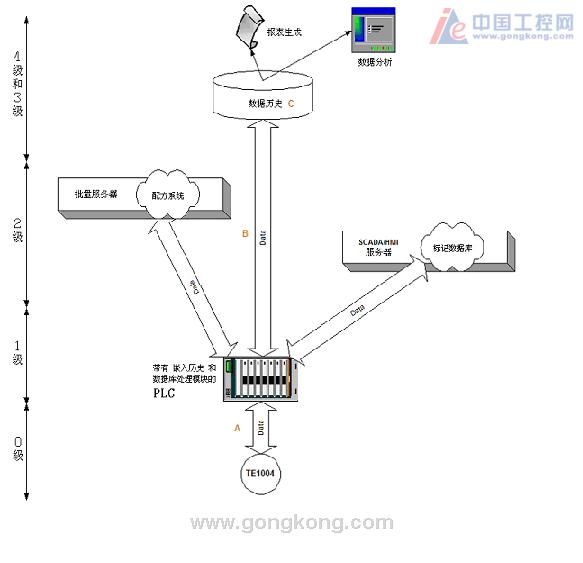
图3 应用直接数据处理模型后的批量控制数据处理示意图
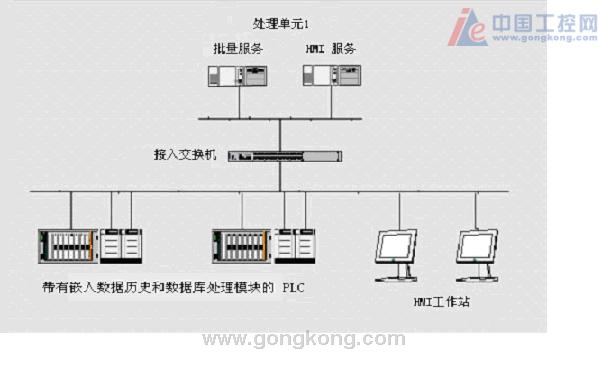
四、展望未来
越来越多的最终用户意识到应该在他们的工厂安装工业级网络组件而不是办公室级组件的必要性。使得硬件基本结构更加健壮的冗余方案和其它方法被采用,并且和硬件相关的故障很有可能会随着时间的流逝而减少。
正好相反的情况出现在过程控制的应用程序端。软件供应商谋求更大、更好和更多数量的应用程序以解决从停机到维护的问题。这里仅仅是突出正确基本结构规划的必要性。仓促地用“软件修复所有问题”很可能会使数据处理的问题更加混乱,它需要越来越多的数据路径和处理点,从而导致更多的潜在故障。
恰似现在的控制工程师要设法管理程序代码,直接数据处理模型的应用最低限度要突出管理数据流和数据处理的需要。正确的管理,对双方而言都是财富,允许可预见的可靠运行。不正确的管理或者是忽视,在可靠性和可维护性方面将成为伴随一生的债务。这些问题还会让管理规范的工厂的控制系统工程技术人员的生活变得一团糟。
直接数据处理模型将是为努力维护和增强控制系统基本结构的控制系统工程师和为简化和提高与设备和过程交互能力的操作人员应运而生的一个有效工具。下表总结的是作者相信在未来五年继续会在工业过程中成为趋势的几个内容。直接数据处理模型支持每个数据处理最小化的趋势。然而只有时间能验证这种观点,它使未来的一些事情值得期待。
目前 |
趋势 |
未来 |
中央数据历史服务器从位于1、2和3级的多个设备、控制器和服务器上采集数据。 |
让数据采集离传感器更近。 |
分布式数据历史服务器与1级控制器集成;使用中央数据历史服务器定时采集分布式历史服务器的缓存。 |
操作人员通过HMI/SCADA子系统与批量控制系统交互;操作人员通过MES子系统与商业系统交互。 | 为所有功能提供单一窗口界面。 | 单一操作界面子系统用一个应用程序显示生产/过程实时数据和显示/输入商用事务数据 |
在普通HMI标记数据库上存储传感器的值,并据此数据库服务其它应用程序(历史、图形、SPC、MES、ERP、Web等等)。 | 数据直接从数据源(生产者)传输到目的地(消费者)。 | 在1级控制器上有单独的数据处理模块,可以把数据传输到2,3,4级上适当的数据库/应用程序中,反之亦然。 |
五、结论
本文所叙述的直接数据处理模型方法,提出了一种批量控制网络设计方案,它在增加可靠性和数据效率的同时,使系统中数据处理的数量最小化。实际的结果通过以下内容完成:列出所有数据生产者和消费者的数据需求,选择允许在数据生产者和消费者之间直接进行数据处理的硬件组件和构建网络体系结构以支持直接数据处理。
这种方法独立于过程类型、仪器总线技术、控制系统的硬件和软件类型或通信协议。用丰富和多样的数据处理、过程控制、批量控制和现今市场上的网络硬件和软件组件,通过应用直接数据处理模型,可以找到适合每个应用需求的解决方案。
参考文献
1.“Enterprise Control System Integration, Part 3: Activity Models of Manufacturing Opera Management”, ANSI/ISA-95.00.03-2005, June 2005.
2. Verhappen, Ian, and Byres, Eric. “Industrial Network Integrity”, Intech, October 2006.
3. Barr, Brian, and McAndrews, Priscilla.“Interprocessor Communication”, Center for theEngineer, Interprocess Synchronization Tutorial, George Mason University, July 1996.